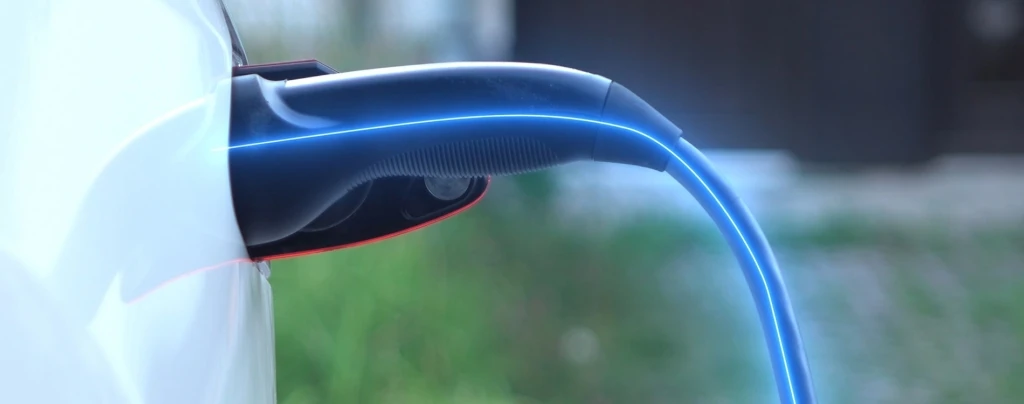
How to Digitise a Long-Standing Company Little by Little
The cable manufacturing experts at LEONI can trace their roots all the way back to 1569. Even though the company, a specialist in supplying the automotive industry and others, is centuries old, it won’t be stopped from working toward breaking into new markets through digitisation. And now they have reached their first milestone: LEONI is using integrated sensors and electronics to make intelligent cables. How? The fathers of these clever cables let us in on their secret when we visited their site.
From ultra-thin glass fibres to cable harnesses as thick as an arm produced for cars or medical devices – you can find almost any cable imaginable at the production sites of this Nuremberg-based company. With all the hustle and bustle going on in the manufacturing halls, I ask myself the following question: why would a company that sells cable systems to customers in the automotive industry, healthcare, factory automation and robotics, and mechanical engineering sectors, with revenues totalling almost five billion euros annually, want to digitise its business? After all, cables have been serving their purpose for over 100 years without digital technology, one would think. But that isn’t always the case. If a cable fails, it usually happens without warning. And when the cable fails, it means production robots, charging stations for e-cars, and power lines also fail.
This is a serious problem for the team of digitisation specialists, led by Torsten Schierholz, Chief Solution Officer at LEONI. His team operates like a technology start-up within corporate structures, and have drawn on their concentrated energy to quickly complete their first project. Their task was to upgrade the existing black box ‘cable’ with integrated sensors and electronics, with the goal of knowing the state of the cable at all times. “Digitisation should not be an end in itself”, explains Schierholz, who gathered experience in the USA and Canada from innovation hubs. “We looked at an existing, serious problem, and decided to use digitisation to solve it”, continues the Chief Solution Officer. On the path to digitisation, LEONI avoided making the one cardinal mistake seen in these types of projects: the project team was allocated sufficient budget and personnel resources, and received enough support from corporate management to be able to develop LEONiQ, the key technology for the production of intelligent cables and cable systems in just over 12 months, which is now ready for the market.
During a Smart Factory roadshow, I eavesdropped on industry experts from A.T. Kearny as they talked about another congenital defect that plagues many digitisation projects in manufacturing in their infancy. Digital experts start working on their projects in a vacuum, without any real connection to the existing core business and its requirements. And this includes production strategy. Torsten Schierholz’s team was able to avoid this pothole too. For one thing, all of the team members are experts in cable systems. For another, they always work hand-in-hand with the company’s production and development specialists. The innovations, designed by the team of over 50 digital experts, are always in line with the production strategy. That makes the digitisation of LEONI an evolutionary process and not a difficult-to-control revolutionary process – integration within a digital ecosystem offering added value along the entire value chain.
The result? Thanks to LEONiQ, any cable used in a system can be monitored through integrated sensors and electronics, irrespective of the time and location. Find out more about what the electronics have achieved and the role the cloud plays in all of this by reading our full-length case study with video.