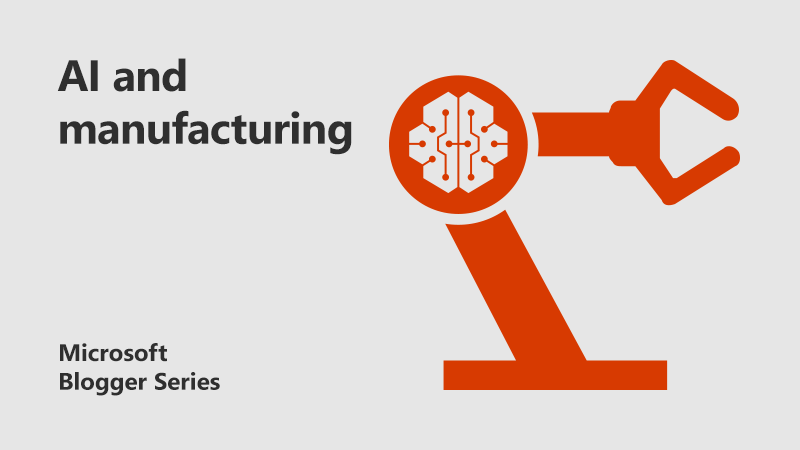
State of the Nation: AI and manufacturing
Manufacturing contributes around 11% to the global economy, and despite contrarian perceptions, the UK manufacturing scene remains robust and growing, with the UK still the 8th largest industrial nation in the world.
Despite a minor slow-down at the turn of the year, primarily triggered by the political uncertainties in UK and ongoing global economic pessimism, the country’s manufacturing industry seems back on the track for growth. According to Microsoft’s AI research report, ‘Accelerating Competitive Advantage with AI’, both investment and employment are on the rise. Meanwhile, the UK government’s 2019 Industrial Strategy initiative will see £110 million of funding injected into AI development for the sector.
Our manufacturing is a global leader when adopting emerging digital transformation strategies such as AI, with the report revealing more than half of UK manufacturers (51%) are currently using AI to some degree, an increase of 3% since 2018. However, the sector faces challenges regarding the pace and scale of AI adoption.
Allaying Fears
A key challenge the sector faces is the fear among unions and workers about the risks automation poses to jobs, despite acknowledgement that these emerging technologies could give the much needed boost to productivity and safety. These concerns must be addressed and allayed if the industry is to truly move forward on its AI-led digital transformation.
The AI research report provides some interesting insights: we see more than half of UK manufacturing leaders (54%) saying they don’t understand how their organisation’s AI solutions arrive at their conclusions, while 51% admit they would not know what to do if they ever disagreed with their AI’s recommendations. Although lower than the national average (63% and 57% respectively), this still leaves a lot of room for uncertainty – and improvement – especially as UK manufacturers try to build on the positive beginnings and move towards becoming fully AI-enabled organisations.
Strong industry leadership is essential. Business leaders must to immerse themselves in the technology, fully getting to grips with how it works, where in the value chain it can be most beneficial, and what to do when teething problems or conflicts occur.
This challenge is appropriately described in the words of Mark McNally, Challenge Director UK Research and Innovation:
‘Leaders need to understand what you hope to achieve and what steps you need to take to get there. The capabilities of AI are growing, but you need to know what you are trying to fix before implementing anything. The danger is having a technology solution looking for a problem. The capabilities of AI are growing, but you need to know what you are trying to fix before implementing anything.’
An internal disconnect
Alongside the operational challenges, there’s also an important cultural impact to consider. In a sector where automation is increasingly commonplace, workers continue to feel uncomfortable about the effect this may have on their job roles. If leaders cannot communicate where, why, and how their organisation’s AI solutions are working, it’ll be difficult to create a culture where workers are empowered to re-skill. Teams need to participate and work alongside machines, rather than feel threatened by them.
Our research indicates a situation in which leaders are not telling and staff are not asking. 95% of staff say they’ve never been consulted by their boss about the introduction of AI. In the same vein, 85% of leaders claim workers have never approached them about AI either. And when asked if teams in their organisation are able to share knowledge and experiences from using the technology to help each other, 39% of manufacturing leaders said ‘yes,’ but only 26% of staff agreed.
The way ahead
Richard King, Sales Director, Manufacturing at Microsoft UK, explains a roadmap for the way ahead.
‘For manufacturers, there are broadly four stages of the AI journey: driving visibility and insights; creating predictability; automation and being prescriptive; and being cognitive and autonomous. Currently, organisations tend to be largely operating at stage one. So, to derive full value from AI, they need to start accelerating their progress. And that is as much about a cultural transformation as it is a technological one.’
It seems, then, that the biggest barriers to the UK manufacturing industry’s move through King’s ‘four stages’ and into full AI implementation at scale are more cultural than technical.
Staff at all levels need a chance to re-skill and help shape the technology’s impact on their day-to-day work. Employees on the front-line need reassurance about their future job prospects in an automating sector. And communication needs to flow freely in both directions to foster a culture of collaboration, inclusiveness and responsible use.
As Nancy Rowe, Head of Inclusion & Diversity at digital transformation firm Publicis Sapient, puts it:
‘From a structural perspective, organisations must instil processes for educating leaders, managers and employees across the business. They have to know what inclusion looks like, then help people build the skills required to be an inclusive manager or team member.’
Meanwhile, Rina Ladva, Sector Director Manufacturing & Resources UK appropriately summarises the next steps:
‘In an industry that, compared to others, is forging ahead on its AI-led digital transformation, it is vital organisations ensure they know exactly what problems they are trying to solve while keeping their eyes firmly fixed on the humans too.’
If UK manufacturing factors in these insights, it will be well positioned to achieve its vision of being among the largest five manufacturing and industrial nations globally by 2021.