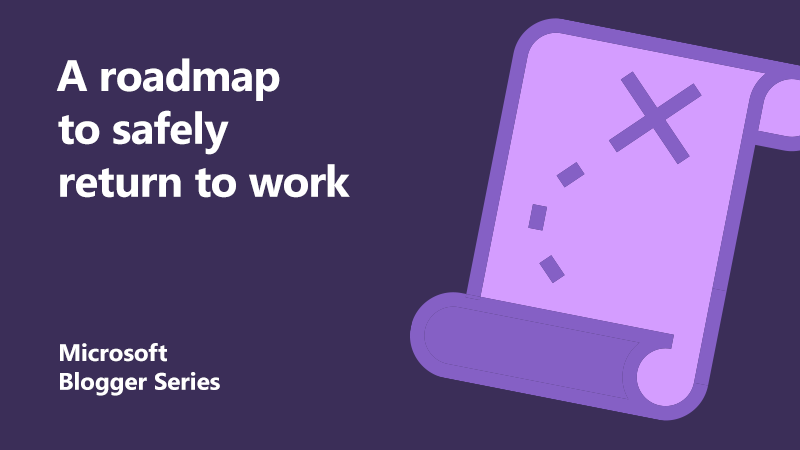
A roadmap for recovery: How manufacturers can return to work safely
As the COVID-19 lockdown starts to ease, we’re beginning to re-start our in-person connections as small social circles are able to reunite. At the same time, in the world of commerce, leaders are considering the safest ways to take the next steps forward and start the return to work.
Within the manufacturing industry, in particular, this challenging period has revealed some uplifting stories of collaboration. Many businesses are working hard to help the wider community, sometimes in partnership with their day-to-day competitors.
For example, Ford, GE, and 3M pledged to pool their resources and expertise to help make ventilators, respirators, and other medical equipment. Toyota did the same, while supporting patient transportation and even drug development and infection-control research.
Microsoft has also played its part, working with a consortium of major industrial, technology, and engineering companies to help produce medical ventilators for the NHS, as part of the VentilatorChallengeUK.
[msce_cta layout=”image_center” align=”center” linktype=”blue” imageurl=”http://approjects.co.za/?big=en-us/industry/blog/wp-content/uploads/sites/22/2020/06/STI-employees-with-assembled-ventilators.jpg” linkurl=”http://approjects.co.za/?big=en-gb/about/ventilator-challenge/” linkscreenreadertext=”Find out more about the Ventilator Challenge” linktext=”Find out more about the Ventilator Challenge” imageid=”37458″ ][/msce_cta]
Return to work
Reflecting on recent events and the prospect ahead, whilst appreciating that this is not an easy time for many, we can also see exciting new opportunities for the manufacturing industry. With a change of perspective and smart decision-making, manufacturers can potentially recover faster, build resilience, and drive future innovation.
In a spirit of partnership, we feel that an approach to recovery could be broken into three chronological phases:
Traditionally, the manufacturing sector has not been an early or keen tech adopter. But if we can learn anything from the current situation, it’s that digital transformation is now an imperative, not an option. To ensure a safe and secure return to work, each of these phases should be seen as a core part of your wider digital transformation journey.
But what does each phase really mean for you and your workforce in the post-lockdown period?
‘Navigate the now’ means what it says – business continuity is your number one objective. You can help enable this by freeing your employees to easily work, collaborate and service customers remotely.
‘Plan the comeback’ involves creating safe working environments and agile factories, with more resilient, responsive, and transparent supply chains.
The third phase, ‘Shape the new normal’, looks ahead. It includes using cloud technologies like Azure and powerful new apps to gain a competitive edge by freeing up creativity and delivering new services.
Learning from the challenge
The VentilatorChallengeUK required consortium partners to work together rapidly to create and ship life-saving medical products. They needed to coordinate supply chains, set up new processes, make components, share new training content, and deliver the products at scale.
Setting aside the unique circumstances, this experience showed how, when needed, we can come together with the help of digital technology to support operations while controlling business costs.
For example, Microsoft HoloLens headsets enabled consortium employees to be trained rapidly, while keeping at a safe distance from each other. Operatives could rapidly get more help from off-site experts using hands-free video-calling through Microsoft Dynamics 365 Remote Assist.
The coordination of multiple suppliers was handled by Dynamics 365 Supply Chain Management, which helped identify over 800 constituent parts.
This pragmatic approach can help businesses cut time and expense while accelerating output beyond customer expectations. In this case, the consortium was able to ship 1,500 ventilators in three weeks.
Building for success: Five pillars
While Microsoft is often initially thought of as a software developer, we’re also a major product manufacturer. In fact, we ship 42,000 SKUs from 33 facilities to over 100 global subsidiaries and retail locations.
It’s therefore appropriate that the consortium’s success – along with lessons learnt from our own experience as a manufacturer – have helped us see new ways forward. I share these ideas with you here in the belief that they may help you drive greater resilience, stronger operations and ultimately more orders.
-
Transforming the workforce
When lockdown began, we made Microsoft Teams widely available, including to the NHS. While enabling business continuity, Teams also empowers employees to work at their very best wherever they might be located. One customer saw Teams usage rise from zero to 35,000 users in a week, then up to 80,000 in three weeks.
-
Engage customers in new ways
Cloud-based cognitive services, such as Microsoft’s Healthcare Bot, have helped healthcare institutions to significantly reduce their workloads. It can cut call volumes by up to 50 percent. This has freed caregivers to focus on treating patients rather than fielding incoming requests.
-
Create more resilient supply chains
The ventilator consortium also brought together Microsoft partners to quickly build and oversee their supply chain within a few weeks. Using Dynamics 365 and PowerApps, our Supply Chain Control Towers and dashboards quickly provided cross-consortium supply chain visibility. This powerful technology can cut inventory investment by 10 percent and boost planning efficiency by up to 60 percent.
-
Build more agile factories
Making processes more agile is a big opportunity. This explains why IDCs 2020 manufacturing trends report says, 60 percent of manufacturers plan to shift their focus from technology to process change management by 2022. For example, you could automate tasks with Dynamics 365. You could also create a ‘digital twin’ of your site to easily monitor and optimise resources, processes, and data.
-
Unlock innovation and deliver new services
All businesses are becoming digital businesses: According to IDC, 70 percent of manufacturers will create 50 percent of new products and services using cloud-based innovation platforms. This would come as no surprise to our consortium partners. They worked seamlessly across three clouds, with data enabling smarter decisions at every step. In fact, the VentilatorChallengeUK itself stands as an exciting case study of what the cloud can help manufacturers achieve.
Despite the turbulence of our times, we remain focused on helping you stay productive, successful, and inspired to achieve more as you return to work. That’s why we’ll be extending this blog into a mini-series. Each one will look at how digital transformation is helping businesses like yours go from strength to strength.
Please check in next week for our next instalment.
Find out more
Join the Microsoft Manufacturing Summit and see how to build a resilient and sustainable future
Learn how to support resilient operations
About the author
Richard is responsible for leading Microsoft’s approach into the UK Manufacturing industry.
Richard joined Microsoft 14 years ago, where he has held various leadership roles across the business, the most recent of which is to establish and drive Microsoft’s strategy into the UK Industrial sector. He works closely with businesses and partners across automotive, aerospace, and manufacturing focussing on how digital transformation can enable them to achieve more.
He also works closely with associated industry bodies and consortia, supporting industry collaboration, growth and skills development.
Richard holds a Bachelor of Arts Degree in Accounting.